6-axis controller for hexapods, TCP/IP, RS-232, benchtop device, incl. control of two additional axes, EtherCAT® interface
C-887.53x Hexapod Motion Controller with EtherCAT®
Control a 6-Axis Positioning System via Fieldbus Interface
- Integration into an automation system
- Synchronous motion in 6 axes
- Cycle time ≥ 1 ms
- Commanding in Cartesian coordinates
- High-resolution analog inputs and motion stop as an option




Digital controller with EtherCAT fieldbus interface
Digital controller for hexapods (6-axis parallel kinematics). In addition, the motor drivers for two further single axes can be controlled. For operation in an EtherCAT network, a higher-level programmable logic controller (PLC) is required on the user side (EtherCAT master with CoE protocol). Operation without PLC is possible via TCP/IP or RS-232. The controller then corresponds to a C-887.52x in terms of functionality and is controlled with the GCS 2.0 command set.
Functions
The position is entered in Cartesian coordinates from which the controller calculates the control of the kinematics. To simplify integration of the hexapod, the coordinate systems (Work, Tool) can be changed. The pivot point can be freely defined. A data recorder can record operating data, e.g., motor control, velocity, position, or position error. The execution of macros and Python scripts on the controller enables stand-alone operation. The controller supports all currently available standard hexapods from PI and, in addition, customer-specific parallel kinematics.
Interfaces
EtherCAT fieldbus interface. TCP/IP for network-based control and maintenance. RS-232. USB port for manual control unit.
Additional interfaces (depending on version):
- High-resolution and extremely fast analog inputs which are ideal for fast alignment routines
- Connection for a motion stop button that activates/deactivates the 24 V output for the hexapod
Optional
- Control via manual control unit
Software support (for control via GCS)
For example, PIMikroMove user software enables fast alignment routines to be depicted graphically. Extensive set of drivers, e.g., for use with C, C++, C#, NI LabVIEW, MATLAB, and Python. PIHexapodEmulator for virtual startup and operation without hardware.
Scope of delivery
The scope of delivery includes the controller, a software package, and a power adapter for the power supply. It is recommended to order the hexapod mechanics and a suitable cable set together with the controller so that the components can be adapted to each other. A PLC master controller is not included in the scope of delivery!
Specifications
Specifications
Basics | C-887.53 | C-887.531 | C-887.532 | C-887.533 | |
---|---|---|---|---|---|
Axes/channels | 6 | 6 | 6 | 6 | |
Additional axes | 2 single axes | 2 single axes | 2 single axes | 2 single axes | |
Processor | Intel Atom dual core (1.8 GHz) | Intel Atom dual core (1.8 GHz) | Intel Atom dual core (1.8 GHz) | Intel Atom dual core (1.8 GHz) | |
Application-related functions | Controller macros GCS ǀ Controller macros PIPython ǀ Data recorder ǀ Startup macro | Controller macros GCS ǀ Controller macros PIPython ǀ Data recorder ǀ Fast alignment ǀ Startup macro | Controller macros GCS ǀ Controller macros PIPython ǀ Data recorder ǀ Startup macro | Controller macros GCS ǀ Controller macros PIPython ǀ Data recorder ǀ Fast alignment ǀ Startup macro | |
Protective functions | Switch-off of the servo mode in case of an error | Switch-off of the servo mode in case of an error | Switch-off via an external switch ǀ Switch-off of the servo mode in case of an error | Switch-off via an external switch ǀ Switch-off of the servo mode in case of an error | |
Configuration management | reading the ID chip ǀ manual parameter input | reading the ID chip ǀ manual parameter input | reading the ID chip ǀ manual parameter input | reading the ID chip ǀ manual parameter input | |
Supported ID chip | ID chip 2.0 | ID chip 2.0 | ID chip 2.0 | ID chip 2.0 | |
Motion and Control | C-887.53 | C-887.531 | C-887.532 | C-887.533 | |
Supported sensor signal | A/B quadrature, RS-422 ǀ BiSS-C | A/B quadrature, RS-422 ǀ BiSS-C | A/B quadrature, RS-422 ǀ BiSS-C | A/B quadrature, RS-422 ǀ BiSS-C | |
Closed-loop values | Position | Position | Position | Position | |
Maximum control frequency (servo cycle) | 10000 Hz | 10000 Hz | 10000 Hz | 10000 Hz | |
Motion types | Point-to-point motion with profile generator ǀ Cyclic transfer of target positions ǀ Area scan routines ǀ Gradient search routines ǀ Wave generator | Point-to-point motion with profile generator ǀ Cyclic transfer of target positions ǀ Area scan routines ǀ Gradient search routines ǀ Wave generator | Point-to-point motion with profile generator ǀ Cyclic transfer of target positions ǀ Area scan routines ǀ Gradient search routines ǀ Wave generator | Point-to-point motion with profile generator ǀ Cyclic transfer of target positions ǀ Area scan routines ǀ Gradient search routines ǀ Wave generator | |
Motion coordination | Coordinated multi-axis motion ǀ User-defined coordinate systems ǀ Work-and-tool coordinate systems | Coordinated multi-axis motion ǀ User-defined coordinate systems ǀ Work-and-tool coordinate systems | Coordinated multi-axis motion ǀ User-defined coordinate systems ǀ Work-and-tool coordinate systems | Coordinated multi-axis motion ǀ User-defined coordinate systems ǀ Work-and-tool coordinate systems | |
Reference switch input | TTL | TTL | TTL | TTL | |
Limit switch input | TTL | TTL | TTL | TTL | |
Interfaces and Operation | C-887.53 | C-887.531 | C-887.532 | C-887.533 | |
Communication interfaces | EtherCAT slave ǀ RS-232 ǀ TCP/IP ǀ USB (only for manual control units) | EtherCAT slave ǀ RS-232 ǀ TCP/IP ǀ USB (only for manual control units) | EtherCAT slave ǀ RS-232 ǀ TCP/IP ǀ USB (only for manual control units) | EtherCAT slave ǀ RS-232 ǀ TCP/IP ǀ USB (only for manual control units) | |
On/off switch | Hardware switch on/off | Hardware switch on/off | Hardware switch on/off | Hardware switch on/off | |
Display and indicators | Status LED ǀ Error LED ǀ Power LED ǀ Macro LED | Status LED ǀ Error LED ǀ Power LED ǀ Macro LED | Status LED ǀ Error LED ǀ Power LED ǀ Macro LED | Status LED ǀ Error LED ǀ Power LED ǀ Macro LED | |
Manual control(s) | Manual control unit with USB interface | Manual control unit with USB interface | Manual control unit with USB interface | Manual control unit with USB interface | |
Command set | GCS 2.0 | GCS 2.0 | GCS 2.0 | GCS 2.0 | |
User software | PIMikroMove | PIMikroMove | PIMikroMove | PIMikroMove | |
Software - APIs | C, C++, C# ǀ MATLAB ǀ NI LabView ǀ Python | C, C++, C# ǀ MATLAB ǀ NI LabView ǀ Python | C, C++, C# ǀ MATLAB ǀ NI LabView ǀ Python | C, C++, C# ǀ MATLAB ǀ NI LabView ǀ Python | |
Analog inputs | 4 | 6 | 4 | 6 | |
Analog input signal | 4 x -10 to 10 V, 12 bit | 2 x -5 to 5 V, 16 bit, 5 kHz bandwidth ǀ 4 x -10 to 10 V, 12 bit | 4 x -10 to 10 V, 12 bit | 2 x -5 to 5 V, 16 bit, 5 kHz bandwidth ǀ 4 x -10 to 10 V, 12 bit | |
Digital inputs | 4 | 4 | 4 | 4 | |
Digital input signal | TTL | TTL | TTL | TTL | |
Digital outputs | 4 | 4 | 4 | 4 | |
Digital output signal | TTL | TTL | TTL | TTL | |
Industrial Ethernet protocol | EtherCAT | EtherCAT | EtherCAT | EtherCAT | |
EtherCAT device class | EtherCAT slave | EtherCAT slave | EtherCAT slave | EtherCAT slave | |
EtherCAT communication profile | CAN application protocol over EtherCAT (CoE) | CAN application protocol over EtherCAT (CoE) | CAN application protocol over EtherCAT (CoE) | CAN application protocol over EtherCAT (CoE) | |
Drive profile implemented for EtherCAT | CiA402 drive profile (IEC 61800-7-201) | CiA402 drive profile (IEC 61800-7-201) | CiA402 drive profile (IEC 61800-7-201) | CiA402 drive profile (IEC 61800-7-201) | |
Supported operating modes according to CiA402 | Homing mode ǀ Cyclic synchronous position mode (CSP) ǀ Safe basic state for activating coordinate systems (no mode changes / no mode selected) | Homing mode ǀ Cyclic synchronous position mode (CSP) ǀ Safe basic state for activating coordinate systems (no mode changes / no mode selected) | Homing mode ǀ Cyclic synchronous position mode (CSP) ǀ Safe basic state for activating coordinate systems (no mode changes / no mode selected) | Homing mode ǀ Cyclic synchronous position mode (CSP) ǀ Safe basic state for activating coordinate systems (no mode changes / no mode selected) | |
EtherCAT cycle time | ≥1 ms | ≥1 ms | ≥1 ms | ≥1 ms | |
EtherCAT synchronization modes | Distributed clocks (DC) ǀ Synchronous with SYNC0 event | Distributed clocks (DC) ǀ Synchronous with SYNC0 event | Distributed clocks (DC) ǀ Synchronous with SYNC0 event | Distributed clocks (DC) ǀ Synchronous with SYNC0 event | |
Electrical Properties | C-887.53 | C-887.531 | C-887.532 | C-887.533 | |
Output voltage | 24 V | 24 V | 24 V | 24 V | |
Peak output current | 6000 mA | 6000 mA | 6000 mA | 6000 mA | |
Miscellaneous | C-887.53 | C-887.531 | C-887.532 | C-887.533 | |
Connector hexapod power supply | M12 4-pole (f) | M12 4-pole (f) | M12 4-pole (f) | M12 4-pole (f) | |
Connector hexapod data transmission | HD D-sub 78 (f) | HD D-sub 78 (f) | HD D-sub 78 (f) | HD D-sub 78 (f) | |
Connector additional axes | D-sub 15 (f) | D-sub 15 (f) | D-sub 15 (f) | D-sub 15 (f) | |
Connector analog input | HD D-sub 26 (f) | BNC ǀ HD D-sub 26 (f) | HD D-sub 26 (f) | BNC ǀ HD D-sub 26 (f) | |
Connector digital input | HD D-sub 26 (f) | HD D-sub 26 (f) | HD D-sub 26 (f) | HD D-sub 26 (f) | |
Connector digital output | HD D-sub 26 (f) | HD D-sub 26 (f) | HD D-sub 26 (f) | HD D-sub 26 (f) | |
Connector motion stop button | — | — | M12 8-pole (f) | M12 8-pole (f) | |
Connector TCP/IP | RJ45 socket, 8P8C | RJ45 socket, 8P8C | RJ45 socket, 8P8C | RJ45 socket, 8P8C | |
Connector RS-232 | D-sub 9 (m) | D-sub 9 (m) | D-sub 9 (m) | D-sub 9 (m) | |
Connector EtherCAT | RJ45 socket, 8P8C | RJ45 socket, 8P8C | RJ45 socket, 8P8C | RJ45 socket, 8P8C | |
Connector for supply voltage | M12 4-pole (m) | M12 4-pole (m) | M12 4-pole (m) | M12 4-pole (m) | |
Operating voltage | 24 (ext. power adapter included) V | 24 (ext. power adapter included) V | 24 (ext. power adapter included) V | 24 (ext. power adapter included) V | |
Power adapter | Included in the scope of delivery ǀ Power adapter 24 V DC | Included in the scope of delivery ǀ Power adapter 24 V DC | Included in the scope of delivery ǀ Power adapter 24 V DC | Included in the scope of delivery ǀ Power adapter 24 V DC | |
Maximum current consumption | 8 A | 8 A | 8 A | 8 A | |
Operating temperature range | 5 to 40 °C | 5 to 40 °C | 5 to 40 °C | 5 to 40 °C | |
Overall mass | 2800 g | 2800 g | 2800 g | 2800 g |
Downloads
Product Note
Product Change Notification C-887.5xx Labeling
Datasheet
Documentation
User Manual A000T0079
PI Simulation Models for CoppeliaSim / V-REP
User Manual C887T0036
C-887.MC2 Manual Control Unit
User Manual MS244
C-887 Hexapod Controller, Models C-887.52, C-887.521, C-887.522, C-887.523, C-887.53, C-887.531, C-887.532, C-887.533
User Manual C887T0011
EtherCAT Interface of C-887 Hexapod Controllers
Technical Note C887T0021
Motion of the Positioner. Position and Orientation in Space, Center of Rotation.
User Manual C887T0007
Description of Coordinate Systems for Hexapod Microrobots and Parallel-Kinematic Positioners
User Manual E712T0016
Fast Multi-Channel Photonics Alignment of Silicon Photonics Components with F-712 Alignment Systems and Hexapods from PI. PILightning Option for First Light Search
User Manual C887T0001
Description of PIHexapodEmulator software
3D Models
C-887.53x 3D Model
Software Files
C-990.CD1 Releasenews
PI Software Suite C-990.CD1
General Software Documentation
User Manual A000T0075
Implementing a C-887 PI Controller in TwinCAT 3.1
User Manual A000T0028
Updating PI Software with PIUpdateFinder
Software Manual SM146
GCS Array Data Format
Software Manual SM148
PIMikroMove
Software Manual SM151
PI GCS DLL
Software Manual SM155
PI MATLAB Driver GCS 2.0
Software Manual SM156
PIStages3Editor for editing the PIStages3 database
User Manual A000T0067
Information on the PIStages3 database. What must be considered when changing from PIStages2 to PIStages3.
Software Manual SM157
PIPython - Programming PI Controllers with Python
Software Manual SM158
PI GCS2 Driver Library for NI LabVIEW
Technical Note A000T0089
PI Software on ARM-Based Platforms
User Manual SM163
PIVirtualMove. Simulation program for parallel-kinematic multi-axis systems
User Manual SM164
Updating controller firmware with PIFirmwareManager
White Paper
Controlling Hexapods via EtherCAT®
Easy Integration of Six-Axis Robots into the Process Environment
Ask for a free quote on quantities required, prices, and lead times or describe your desired modification.
6-axis controller for hexapods, TCP/IP, RS-232, benchtop device, incl. control of two additional axes, EtherCAT interface, analog inputs
6-axis controller for hexapods, TCP/IP, RS-232, benchtop device, incl. control of two additional axes, EtherCAT interface, motion stop
6-axis controller for hexapods, TCP/IP, RS-232, benchtop device, incl. control of two additional axes, EtherCAT® interface, motion stop, analog inputs
견적 요청 방법
Ask an engineer!
Quickly receive an answer to your question by email or phone from a local PI sales engineer.
기술
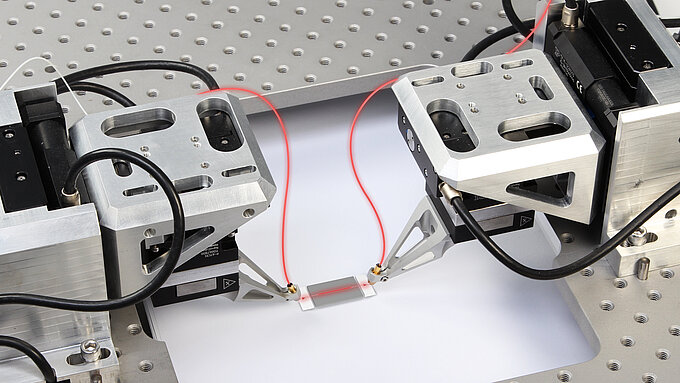
Active Alignment
The need to align devices down to nanoscale accuracy is arising in many fields. Optical components such as the lenses or lens assemblies in small cameras, or even the CCD chip itself, need to be positioned with ever more precision.
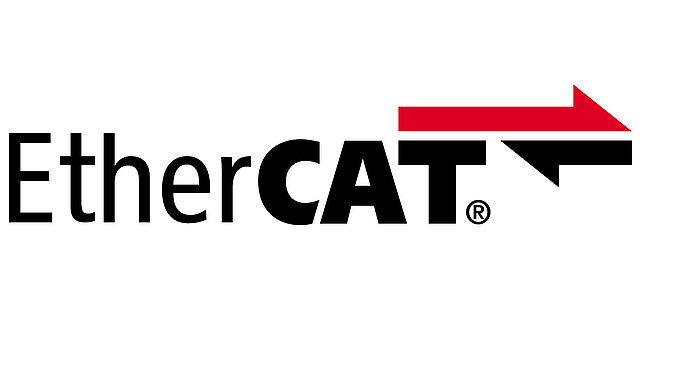
EtherCAT Connectivity of PI Products
PI offers high-precision drives for use as EtherCAT slave, or integrates with ACS Motion Controllers as Master, or 2nd Master in an existing architecture.
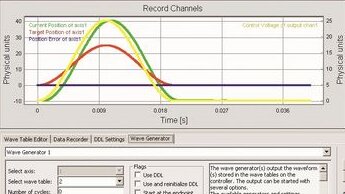
Digital Motion Controllers
Digital technology opens up possibilities for improving performance in control engineering which do not exist with conventional analog technology.
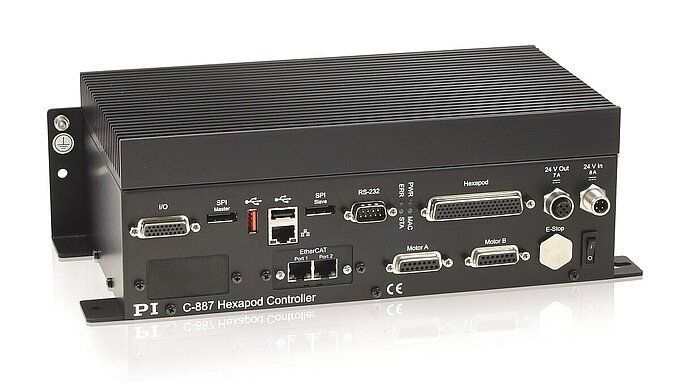
Digital & Analog Interfaces
Fast USB or TCP/IP interfaces as well as RS-232 are the standard interfaces supported by modern digital controllers from PI. Furthermore, PI also provides digital or analog real-time capable interfaces.